A state-of-the-art industrial cleaning
Cleaning is essential in people’s daily lives to ensure optimum health and overall well-being. Not only that, but it is also a vital procedure needed in different industries.
Industrial facilities, particularly, have cleaning as an imperative process in manufacturing for its products and various parts and devices. Traditional cleaning methods may involve manual labour, harsh chemicals, and mechanical scrubbing, and environmental regulations make such processes less attractive. Products and parts with complex shapes and crevices are hard to clean, and traditional cleaning can be time-consuming and expensive.
Ultrasonic cleaning has become a popular alternative which different manufacturing facilities employ. This method is efficient in lowering cleaning time and operational costs. Companies and workshops with cleaning needs for complex parts use ultrasonic cleaning for its technology and benefits.
For more than 50 years, the research and development of ultrasonic cleaning technology have resulted in multiple ultrasonic cleaners available today. Choosing a suitable cleaning machine is essential to yield the best result. Key cleaner characteristics include the frequency, ultrasonic and heating power, type of transducer, and unit tank size. It is also essential to know how ultrasonic cleaners work, their benefits, and their applications.
What Is Ultrasonic Cleaning?
Many types of cleaning solutions are available in the market today. One of the most popular and sophisticated is ultrasonic cleaning. Using an ultrasonic cleaner is cost-effective, time-efficient, and ecological.
Ultrasound waves are produced by transducers and generators that pass through an elastic medium such as liquids. Liquids are appropriate in this cleaning type as it infiltrates submerged items and allows surface cleaning even with complex and hard-to-reach parts.
The transducer creates high-frequency ultrasonic waves, which result in the rapid changes of pressure in the liquid that produce imploding microscopic bubbles; this is called the cavitation effect. The agitated microscopic bubbles in the cleaning liquid solution make mechanical action to remove surface contaminants on the submerged item.
During the pulsation of the micro-currents, the heat produced also helps the removal of contaminants. A cleaning liquid solution also aids in a better cleaning result. This cleaning method is efficient for machines and parts used in automotive manufacturing and workshops, electronics service shops, aerospace and marine parts manufacturing, railway, assembly lines, and other manufacturing industries.

Ultrasonic Technology
Ultrasonic Waves
Sound is the transmission of vibrations through an elastic medium which can be a solid, liquid, or gas. Sound wave generation is when a single or repetitive motion produces a sound wave in a conducting medium, such as a vibratory movement. The air movement through the cone of a radio speaker is an excellent example of vibratory sound waves produced by mechanical motion.
On the other hand, ultrasound is the science of sound waves that goes beyond the limits of human hearing. The frequency of sound waves determines its timbre or pitch. Low frequencies produce bass or lows. High frequencies have high or treble tones. These frequencies have a massive part in ultrasonic cleaning, which will be discussed further below.
These sound waves that travel through and agitate the cleaning liquid solution lead to cavitation that causes erosion of the surface contaminants.
The increasing demand for cleanliness has led to complex technologies, especially in the last decade. Today it is possible to customise ultrasound to optimise effects in various applications. Using ultrasound in cleaning has been first introduced in the 1950s. Since then, various manufacturing has been developing and improving the technology to what it is now today.
Cavitation
One essential part of an ultrasonic cleaning system is the generator which produces electric high-frequency signals. These signals are transmitted to transducers and are converted into sound waves. When the waves pass through the transducer’s metal plate through the cleaning liquid solution, the waves create low-pressure regions that produce cavitation.
The rapid formation and collapse of vapour bubbles within a liquid forms cavitation. Jets of energy are released during the troughs and collapse at the following wave peaks or wavefronts, forming cavitating bubbles. Wavefronts are imaginary spaces representing the points of a wave that vibrate in unison. As these wavefronts pass, the cavitation bubbles vary in magnitude under the influence of positive pressure, then grow to a varying size.
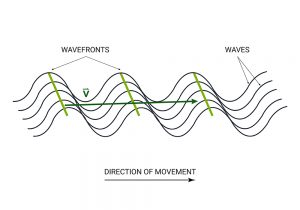
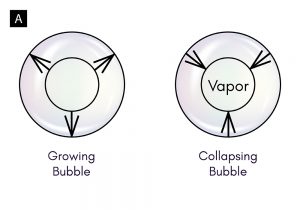

Frequency
In ultrasonic cleaning, different frequencies allow the removal of various particles, which makes the technology flexible in its uses and applications. General cleaning, which is at 40kHz, can remove large chips, weld spatter, swarf, and laser scale. This frequency is used in hardware, plumbing, consumer products, automotive, and aircraft industries.
A low frequency, which is 25kHz and below, will have larger and fewer bubbles which are aggressive in removing particles but gentle in materials. It can remove gross dirt, carbon, sand, scale, mud, and heavy road dirt. Low frequencies are primarily used in off-road remanufacturing, casting, fabrication, and rough machining.
For finer contaminant removal, higher frequency produces smaller cavitation bubbles that can clean the materials faster and more thoroughly. An example is when the frequency is set at 400kHz to 800kHz, it can remove dust, fingerprints, and handling residues. This frequency level is used in disc drives, optical, and electronics.
Temperature
The temperature plays a role in the power of the ultrasonic cleaning action and the effectiveness of the cleaning liquid solutions.
Temperatures are related more to the effectiveness of the cleaning agent in use rather than the effectiveness of the ultrasonic cleaning system. Ideal temperature varies for each ultrasonic cleaning tank and application intended. The average temperature to set the machine is between 55°C and 60°C for basic applications.
The high temperature improves the distribution of ultrasonic cleaning action in the tank. It disperses the microscopic bubbles, lessening the concentration of cavitation energy.
Although the mechanical cleaning action of the ultrasonic cavitation is reduced at elevated temperatures, the improvement in the effectiveness of the cleaning liquid solution can overcome the reduction. Some cleaning liquid solutions work best at high temperatures. By operating the ultrasonic cleaner at these high temperatures, the cleaning liquid solution has an improved ability to loosen the bond between the contaminant and the parts.
Each cleaning liquid solution has an optimum temperature at which it performs best. It is best to check the cleaning liquid solution for its ideal temperature. It is advisable to also have an ultrasonic cleaning system with an adjustable temperature setting when different cleaning liquid solutions would be used.
Cleaning Liquid Solutions
The cleaning liquid solution serves as detergent and is as vital as ultrasonic frequency and power. Most used chemistries fall into mildly alkaline, alkaline, acidic, and neutral categories. Liquid solutions are supplied as concentrates, so the proper liquid solution-to-water ratio is needed for an optimised cleaning cycle. Manufacturers provide dilution and cleaning temperature recommendations.
Multiple cleaning liquid solutions are formulated for different purposes to protect the nature of materials, save money, and achieve optimal performance. One example are mildly alkaline liquid solutions which has three types: 1) Mildly alkaline universal cleaners 2) Special cleaner with ammonia 3) Special cleaner – tenside free. Another kind are alkaline liquid solutions with two types: Alkaline intensive cleaner and demulsifying special cleaner silicate-free. The third kind are neutral cleaning solutions and has two types: neutral cleaner for gentle cleaning and neutral universal cleaners. Lastly, acid liquid solutions that consists of three types: 1) Special gentle cleaner 2) Special intensive cleaner 3) Special demulsifying cleaner.
Many cleaning liquids available in the market are formulated with non-toxic and biodegradable ingredients, making them eco-friendly and disposal easy. Most solutions are water-based, so rusting may be a concern, but rust inhibitors can be added to address this matter.
Ultrasonic Cleaning System
An industrial ultrasonic cleaner has three primary components for the system to function: a generator, transducers, and a tank. Each component is essential to complete an ultrasonic cleaning system, and below discusses these in detail.
Generators
Generators produce the main part of ultrasonic cleaner technology. Ultrasonic generators produce the high-frequency electric signal required for an ultrasonic cleaning system to operate. They control the frequency and ensure that the system’s selected frequency and power output are maintained, which are important.
As mentioned previously, cavitation bubbles form in sound wave pressure troughs and collapse in the pressure crests, creating an intense mechanical cleaning action on the contaminated surfaces of the immersed parts. The transducers placed in the tank create the sound waves through vibrations at the ultrasonic frequency produced by the generators. The whole system has to have complementary characteristics with the frequencies, ultrasonic and heating power, tank size, and controls, forming an integrated approach that works together in a specific cleaning application. Choosing the right generator greatly affects the performance of the entire ultrasonic cleaning system.
The generator has to fit into the production environment while matching the general cleaning application requirements of the user. The operating voltage, the size, and the type of cleaning intended are the factors needed to be considered to find a suitable cleaning system. Determining the frequency, ultrasonic cleaning and heating power, and other controls are essential for each cleaning application. Once the specific cleaning requirements are defined, choosing the right frequency and corresponding transducers and cleaning tanks is clear. Sonixtek ultrasonic cleaners already include appropriate needed generators for better cleaning action.
Generally, low frequencies produce larger cavitating bubbles, resulting in an intense cleaning action for parts or components of more complex materials. Higher frequencies provide gentler cleaning of parts or components made from softer materials than lower frequencies. In all cases, high ultrasonic generator power is required to fill the cleaning tank with ultrasonic waves. The generator must produce a uniform wave pattern for the most effective cleaning action.
Transducers
The second component needed in an ultrasonic cleaning system is transducers. A transducer is a device that converts alternating electrical energy to vibratory mechanical energy. The Sonixtek ultrasonic cleaners provide the appropriate number of transducers according to the size and volume for efficient ultrasonic cleaning.
A transducer comprises an electrical section that receives the electric signal from the ultrasonic generator and a mechanical unit that vibrates at a high frequency to generate sound waves. Ultrasonic cleaners use this technology and transmit these waves through the cleaning fluid, which agitates water molecules, resulting in cavitating bubbles. The transducer converts the electric signal from the generator into a scrubbing action. The collapse of the bubbles scrubs the parts to be cleaned and dislodges dirt and contaminants from the part surface.
Ultrasonic transducers have to withstand the conditions in the cleaning solution without damage. Hence, these devices are enclosed in waterproof stainless-steel boxes to be immune to pitting from exposure to ultrasonic waves. Ultrasonic cleaning solutions are sometimes heated, and they may contain mild solvents. Transducers should continue to deliver rated performance under such operating conditions. Ultrasonic Cleaning transducers provides ultrasonic power in the liquid of the cleaning tank and withstand challenging operating environments without failure or lowered performance.
Tanks
The third component in an ultrasonic cleaning system is a tank. Ultrasonic cleaning tanks hold the cleaning liquid and need it to be made of thick stainless steel to keep higher temperatures and prevent rusting, which Sonixtek conveniently has. When a generator produces the electric signal, the transducer within the tank converts that signal into waves within the cleaning liquid. The part being cleaned is placed inside the tank and immersed in the cleaning solution, and the cavitation bubbles created by the transducers remove all surface contamination.

Cleaning tanks need to withstand the mechanical cleaning action, vibrations, and rising temperatures, and their construction also meets different cleaning requirements.
Standard tank sizes are available on Sonixtek’s inventory to accommodate most cleaning requirements. However, when the ultrasonic cleaning system is a single-use installation, the cleaning tank can be sized to exactly contain the parts usually cleaned. Custom tanks are then the most efficient for long and narrow parts or have odd shapes. Businesses with specific irregular-shaped parts for ultrasonic cleaning also beneficial for a custom tank. Sonixtek can customise the ultrasonic cleaning system, including tanks, frequency, and more.
For ultrasonic cleaning systems used for many different cleaning applications, the size, shape, and even weight of the parts to be cleaned should be carefully considered. The choice of tank is critical not to limit the cleaning system’s flexibility.
When choosing an ultrasonic cleaner, it is best to consider the largest part to be cleaned to accommodate the tank size. It is also highly advisable to have a basket that can hold in the tank for small and delicate parts as this prevents them from coming into contact with vibrating tank sides and bottom.
Vibrations may damage small or delicate parts if they contact the walls or bottom of the cleaning tank. Over time this contact may scratch the tank’s surface when no basket keeps the parts and the tank. Cavitation may occur on these scratches, creating holes and damaging the tank over time. Placing these parts in a basket prevents potential damage. In this case, the basket must be large enough to hold the parts, and the tank must big be enough for the basket. Baskets prevent damage to the tank, so it is crucial for an ultrasonic cleaner. That is why Sonixtek provides a basket for every ultrasonic cleaner.
Ultrasonic Cleaner Features
Sonixtek standard ultrasonic cleaners have additional features to optimise the cleaning process, apart from just the regular mechanical cleaning. Additional features are available for more advanced models, but the sweep and degas modes are basic features found in all our industrial ultrasonic cleaners.
Sweep Mode
Ultrasonic cleaning requires much power distributed across the many transducers affixed to the vertical walls and at the base.
If a generator emits a single fixed frequency, some transducers will not work correctly, resulting in poor performance, quick overheating, and deterioration of the device.
The ultrasonic cleaning generator is equipped with the sweep mode set in the workshop and refined on-site during final testing to avoid these problems. The effective primary central frequency is determined, and how much movement must occur to achieve the resonance of every transducer.
Sweep mode provides a slight variation in ultrasonic frequency to oscillate ultrasonic power, preventing hot spots or areas where intense cavitation occurs, and dead zone, where there is low to no cavitation. Parts are being subjected to a uniform clean with sweep mode operation. Sweep mode prevents damage to extremely delicate parts or reduces the effects of standing waves in cleaning tanks.
Degas Mode
Degas mode is engaged in driving off cavitation-inhibiting trapped air from fresh cleaning liquid solutions. This step can be done in a unit even without a degas mode. Operate a cleaner without a load and set the machine for 10 minutes, and this would rid all entrapped airs and bubbles.
A case in point is the importance of degassing new ultrasonic cleaning solutions before the cleaning or sample prep operations begin. Entrapped air in new solutions will interfere with the cavitation action that performs the cleaning or sample prep process until removed.
Ultrasonic Cleaning Equipment
Ultrasonic cleaning equipment ranges from small tabletop units to massive systems used in various industrial applications. The size of the tank may determine the success of an ultrasonic cleaning application. The most straightforward application may need only a smaller tank. However, there are more sophisticated cleaning systems for industrial cleaning, including rinses, added process tanks, and hot air dryers. Automation is often added to lessen labour and assure process consistency. The largest installations use immersible ultrasonic transducers, which can be mounted on the sides or bottom of cleaning tanks of any size. Immersible ultrasonic transducers offer complete flexibility and ease of installation and service.
Benchtop Ultrasonic Cleaners
Benchtop cleaners are often smaller and commonly used in doctors’ offices and clinics, laboratories, and jewellery stores. The academe also uses tabletop ultrasonic cleaners for research purposes. Other industries which need to clean small and delicate parts also use this.
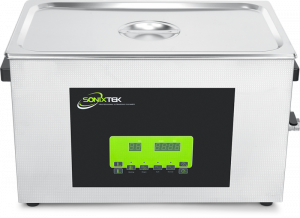
Industrial Ultrasonic Cleaners
Industrial ultrasonic cleaners have more features than tabletop to accommodate intensive industrial cleaning needs. At Sonixtek, there are currently four industrial ultrasonic cleaner series having different additional features.
These industrial ultrasonic cleaners are engineered to withstand intensive industrial cleaning. They have bigger tanks that can hold up to 8000 litres which can clean large parts and machines. Compared to tabletop, these cleaners have sophisticated additional features that supplement ultrasonic cleaning.
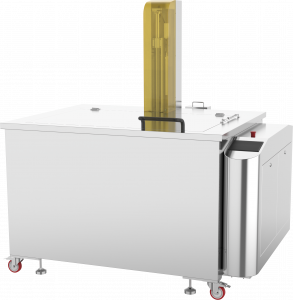
Additional features that Sonixtek included in the industrial ultrasonic cleaners include filtration systems, buffer tanks, and oil separation systems with oil skimmer. The advanced models also include lift systems, integrated laminar flow systems, and a PLC-controlled material handling system.
Customs Units
When the standard industrial ultrasonic cleaner does not meet the cleaning requirements, there is also a wide range of options for custom-designed systems. One of which is a modular system with multi-purpose tanks that combine ultrasonic cleaning function, prewash, rinsing tank, high-pressure jet cleaning, and hot air-dry system.
In choosing the right industrial ultrasonic cleaner, the tank must fit the largest part or machine that needs cleaning, and the system’s power must also be suitable to fill the tank with ultrasonic sound waves. Sometimes custom tanks are needed for objects with an unusual shape to have lesser cleaning solutions and lower power.
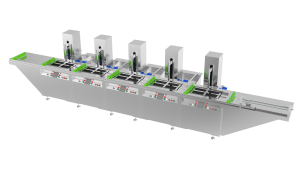
Uses And Application
With the wide range of machines, liquid solutions, and new features available, there are many applications of ultrasonic cleaning technology in different industries, making ultrasonic cleaners versatile and functional.
Industrial Application
Machined parts come out of production with a variety of substance contamination. When parts are processed in machines, traces of lubricants may remain on the part and may pick up dirt across the entire production process; this leaves particles on the surfaces, and such contamination is harmful. Manual scrubbing is time-consuming and may damage and scratch the part surfaces. Ultrasonic cleaning can be used instead with all parts, leaving no residue and damage on metal surfaces. Industrial ultrasonic cleaners provide a cost-effective and efficient solution to meet these cleaning requirements.
Automotive Application
Cleaning different and complicated machines is a time-consuming operation that is part of the daily operation in the automotive industry.
Parts used in automotive manufacturing and re-building, and parts repairs must be cleaned thoroughly before use. New parts used in manufacturing are seldom contaminated, but even these parts may have traces of machining compounds and metallic contamination. Parts used in re-building and repair often have heavy deposits of carbon or grease. Other contaminations in this industry include oil, gasoline remnants, or metallic contamination.
Furthermore, using traditional methods, cleaning these parts involves extended soaking in harsh chemicals, pressure washing to remove heavy contamination, and manual scrubbing and scraping to clean hard-to-reach places. This method of automotive parts cleaning is expensive and time-consuming.
When automotive ultrasonic cleaners are used, parts come out of the cleaning process free from contaminants. An experienced manufacturer can tell on the correct frequency, power, and time to complete the cleaning process. With the right ultrasonic system and timing, even difficult-to-clean places are cleaned down to the original surface. Parts are ready to be used in a final assembly, and output quality is higher.
Electronics Application
Ultrasonic cleaning in electronics saves time and improves results without compromising safety. It is effective for printed circuit boards and electrical assemblies.
This method helps in removing dust, dirt and corrosion from PCBs and other electronic components, which is essential as it impacts the overall performance of the electronic device.
An ultrasonic cleaning system can safely and effectively remove solder paste and flux residues from circuit assemblies. When using an ultrasonic cleaner to clean printed circuit boards after wave soldering, it is easiest to begin soon after the soldering process as long as the board cools below 70°C before starting the ultrasonic PCB cleaning process.
To be alerted of updates for more ultrasonic cleaning information, follow Sonixtek’s Facebook or sign up to our newsletter.